|
|
|
|
HANDCRAFTS |
|
|
|
|
|
|
|
|
Oaxaca is known for its strong artistic heritage. Popular handcrafts include baskets, cotton textiles, jewelers, leatherwork, pottery, stonework, tannery, tin ware, wool tapestries and artifacts made of black clay. These handcrafts are unique because they are hand made and not mass produced. The richness, quality, variety, and prices of its handcrafts make Oaxaca a tourist attraction. |
|
|
|
|
|
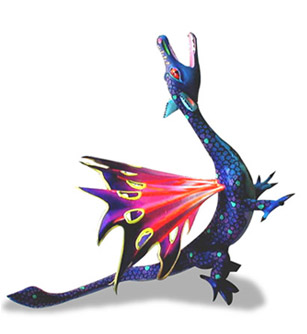 |
Oaxacan Wood Carving (“Alebrijes”)
Wood carving, an ancestral Zapotec tradition, comes to its fullest expression through the Alebrijes. These are imaginary and magic pieces born out of the creativeness and skillful hands of the Oaxaqueño craftsmen.
There are several versions regarding the origin of alebrijes. One of the most accepted ones indicates that they were born in the imagination of Pedro Linares, a native of Arrazola. Suffering from a terrible illness, in his dreams he start having visions of fantastic creatures with fanciful forms that were shouting: "¡alebrijes, alebrijes!" In his nightmares, the creatures emerged from trees, stones and clods in the deepest areas of an immense forest.
Those creatures transformed into animals that had impossible shapes and colors. Those surrealist images were so impressive to him that when he recovered from his illness he started carving them on wood. In 1992, Pedro Linares died not without leaving a legacy of his handcraft style, which has won international prestige. Others claim that it was Manuel Jiménez, who started with this art. |
|
|
|
|
|
|
|
What started as a matching income source soon became the main source of revenue for entire families in the region. Around Oaxaca City, there are three little villages that are entirely devoted to this art: San Antonio Arrazola, San Martin Tilcajete, and La Union Tejalapam.
The wood utilize in the manufacture of these sculptures are green branches of copal (Bursera trees) from the mountains. It is said that the shapes of the branches found on treetops is what inspired the craftsmen to make these fantastic and imaginary characters. Using machetes and razor blades they create figures of animals like lions, jaguars, iguanas, dogs, snakes and birds. Their perfect sculptured makes them unique, and have been consider as pieces of art. |
|
|
|
|
|
|
|
Every artist has its own style of work in terms of themes for the figures, colors, painting etc. Pieces are custom made or in traditional shapes. There are alebrijes of many sizes and designs, but of course, the original ones are more like chimeras. |
|
|
|
|
|
|
|
|
OAXACAN POTTERY |
|
|
|
|
|
|
|
|
|
|
|
|
The manufacturing techniques applied to pottery in Oaxaca are completely primitive using only the traditional techniques. Bruñido Pottery is delicately colored, precisely painted and has intricately stylized design. Production includes casserole dishes, plates, cups, fruit bowls, glazed tiles, jugs, pitchers, pots, vases, jars, tea sets, toys and other decorative articles. Santa Maria Atzompa is a village where craftsmen create the Glassy Pottery through a long and precise process, using a primitive technique that does not use any mold. San Pedro Tlapazola, a small town in the high valleys of the Mixteca region is said to be the origin of the Orange Pottery. Pottery manufacture is the most important
But without a question, black pottery (“barro negro”) is the most traditional technique, around the entire world only made in Oaxaca. Some imitations of this pottery are varnished with black colorants, but the color in the original black pottery is achieved during the cooking. The beauty of this pottery is accomplished by a long process of several working days by Zapotec craftsmen, thus giving its unique final touch. |
|
|
|
|
|
|
|
|
|
Black pottery |
|
|
|
|
|
|
Black pottery is made in San Bartolo Coyotepec, at 20 minutes of Oaxaca City (about 16 km south) on road number 175. This town has a well deserved reputation as an important ceramic center in Mexico. The unique color and texture of this pottery is made with a carefully kept recipe, in part to provide a mystery around it, in part to remain as the only town that makes it with an original style. There are many workshops even on each side of the highway, but some of the more well reputed workshops are in the inner part of the town, some of which have exhibits of throwing.
The black color of this pottery comes after cooking the clay, which originally has the very common reddish clay color. Black pottery is made at low temperatures in a reductive atmosphere with rudimentary ovens specially made with bricks before each cooking.
|
|
|
According to the popular voice, the founder of the technique was Rosa Real de Nieto (1900-1980), an indigenous woman who became almost a hero in the town. This town has been visited by different presidents and other important national and foreigner people.
Black pottery includes cheep products, such as vases, ash trashes, and small figures, but there are also very large pieces (about 80 cms), mainly basins. This pottery has two finishes: glossy or dull. The glossy ones shin with a metallic silver tone, whose invention is attributed to René Pérez. Some of the pieces are perforated and some of them hold candles inside.
|
|
|
|
|
|
|
|
|
|
|
|
|
|
|
|
|
TAPESTRY AND TEXTILES |
|
|
|
|
|
|
|
|
|
Oaxaca is also known for the use of natural products to produce tapestry and textiles. This in part is favored by the great biodiversity that the State hosts. Although natural dyes are extracted from different plants, animals and minerals, most of them are obtained from seeds, leaves, roots, bark and fruits of plants, producing an extraordinary assortment of colors, each one with a distinctive tone. Natural dyes were used in the region even since before the Spanish arrived in the territory, but it was not until they dominated the region when the Dominicans introduced the sheep and the Indians were taught how to process the wool. The Indians were instructed in the use of spinning to more efficiently transform the wool into thread and textile mills.
Therefore, the combination of European techniques with the use of the natural resources of Oaxaca and the use of native motives results in bright very unique and extremely beautiful pieces of art. In this way, the Zapotecas of some towns such as Teotitlán del Valle, Mitla or Tlacolula have a long tradition in the production of fine tapestry. For instance, Teotitlán del Valle is famous for the original and colourful designs of 100% wool rugs. This town is located at about 30 minutes from Oaxaca city, 4km on a deviation towards the north located at 24 km on the federal highway 190 towards Tlacolula.
|
|
|
|
|
|
|
|
|
|
|
|
Colours are obtain from many sources and due to the use of common names it is not always easy to find out what the actual species are. Two very frequently used colours are obtained from animals: the purple is produced from “tishinda”, a marine winkle, while the bright red is usually obtained from an insect, the “grana cochinilla” (Dacylopius coccus Costa), an homopterous that parasites “nopales” (Opuntia spp. and Nopalea spp.) that since prehispanic times has been cultivated for this purposes.
Santa María Coyotepec is a town that one can visit to learn more about this. The insect is dried and grounded and the colour is then extracted. The intense blue is said to be produced from a plant commonly known as “índigo” or “añil” (Indigofera thibaudiana DC. and I. suffruticosa Mill.); the yellow is produced from different plants, which result in different tones; one of the most common ones comes from “huatle” (a dried moss); the amber from lichens that grow on rocks; another tone of yellow is obtained from the peel of the fruit “granada” (Punica granatum L); black is produced from the fruit of “yag gsh be’e” (Prosopis juliflora [Sw.] DC.); brown is obtained from the shell of nuts (possibly Carya illinoinensis [Wangenh.] K. Koch, or Juglans spp.).
|
|
|
|
|
|
|
|
|
|
|
|
Other plant species used as dies are Befaria laevis Benth. (Ericaceae), Bocconia frutescens L. (Papaveraceae), Bursera bipinnata (DC.) Engler, Diospyros oaxacana Standle. (Ebenaceae), Haematoxylon brasiletto Karst (Leguminosae), Justicia ramosa Greenm.) T. F. Daniel (Acanthaceae), Pachycereus marginatus (DC.) Britton et Rose, pitecellobium dulce (Roxb.) Benth. (Leguminosae).
The time required to fabricate a rug varies from two weeks to one year depending on the complexity of the work, the size of the rug and the design. Once the sheep is shear, the wool is washed and dry, then, it is carded and the thread is produced. This thread is then stained in containers that have boiling water with the different dyes and natural fixatives, which prevent the color to be lost. Each dye uses a different fixative. For example, for the blue, people use bleach from ashes; for the red “tejute”; for the black “alcaparrosa” (possibly Cesalpinia coriaria [Jacq.] Willd., Leguminosae); and for the different yellows and brown, vinegar and salt. Once the thread is stained and the color is fixed, it is dried and then the textile mills are used to produce original designs, most of them using prehispanic motives.
|
|
|
|
|
|
|
|
|
|
|
|
|
|